CNC三伤,通常指的是在CNC(计算机数控)加工过程中出现的三种主要损伤:刀具损伤、工件损伤和设备损伤。为了改善这些损伤问题,可以采取以下方案:
1. 刀具损伤改善方案:
优化刀具路径规划,减少刀具与工件的碰撞和摩擦。
选择合适的刀具材料、几何形状和涂层,以提高刀具的耐磨性和切削性能。
定期检查和更换刀具,确保刀具处于良好的工作状态。
采用先进的刀具监测技术,如振动监测、声发射监测等,及时发现刀具异常情况。
2. 工件损伤改善方案:
优化加工工艺参数,如切削速度、进给速度和切削深度等,以减少工件变形和损伤。
选择合适的夹具和定位方式,确保工件的稳定性和加工精度。
采用先进的加工技术,如高速切削、干切削等,以减少工件的热变形和损伤。
定期检查和维修机床,确保机床处于良好的工作状态,减少工件加工过程中的振动和误差。
3. 设备损伤改善方案:
定期对设备进行维护和保养,确保设备处于良好的工作状态。
采用先进的设备监测技术,如温度监测、振动监测等,及时发现设备异常情况。
对设备进行定期检查和维修,确保设备的各个部件正常工作,减少设备故障和损伤。
采用先进的加工技术,如高速切削、干切削等,以减少设备的热变形和损伤。
以上方案可以综合运用,以改善CNC三伤问题,提高加工质量和效率。在机械加工的世界里,CNC(计算机数控)机床扮演着至关重要的角色。它们如同精准的舞者,在金属与硬质合金之间翩翩起舞,创造出令人惊叹的精密零件。即便是这些高科技的宠儿,也难免会遇到一些棘手的问题,这些问题被称为“CNC三伤”——工件过切、分中问题、对刀问题。这些问题不仅影响加工效率,还可能对机床和刀具造成损害。今天,就让我们一起深入探讨这些问题的根源,并寻找改善方案,让你的CNC加工更加顺畅。
工件过切:精加工中的隐形杀手
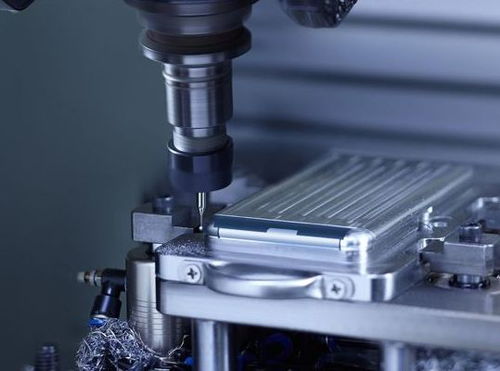
工件过切是CNC加工中常见的问题,它不仅浪费材料,还可能影响零件的最终性能。那么,究竟是什么原因导致了工件过切呢?
首先,刀具的选择至关重要。如果你使用的刀具强度不够,太长或太短,都可能导致刀具在加工过程中发生弹跳,从而造成过切。想象刀具就像舞者的舞鞋,如果尺寸不合适,舞步就会变得笨拙。
其次,操作员的操作也是关键因素。不正确的操作会导致刀具路径偏离预定轨迹,进而引发过切。这就好比开车,如果方向盘不掌握好,车子就会偏离车道。
再者,切削余量不均匀也是导致工件过切的重要原因。比如,曲面侧面留0.5毫米,底面只留0.15毫米,这种不均匀的余量会导致加工深度不一致,从而产生过切。
切削参数设置不当也会引发工件过切。比如,公差设置太大,或者SF(进给率)设置得太快,都会导致刀具在加工过程中过度切削。
那么,如何改善工件过切问题呢?其实,解决方法并不复杂。
首先,选择合适的刀具至关重要。记住,用刀原则是“能大不小、能短不长”。这意味着,选择刀具时要尽量选择长度适中的刀具,避免过长或过短。
其次,添加清角程序,尽量使余量均匀。比如,侧面和底面的余量应该保持一致,这样可以避免加工深度不一致导致的过切。
再者,合理调整切削参数。余量较大的拐角处可以适当修圆,这样可以减少刀具的冲击力,避免过切。
利用机床的SF功能,操作员可以微调进给速度,使机床切削达到最佳效果。
分中问题:精准定位的难题
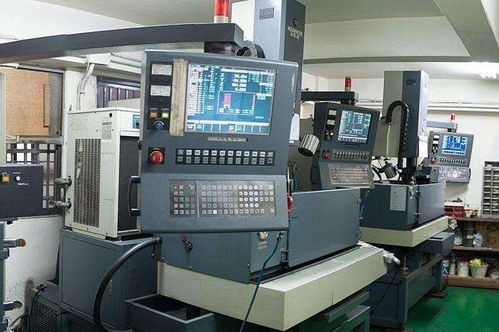
分中问题是CNC加工中另一个常见的问题,它直接影响加工的精度。那么,分中问题究竟是如何产生的呢?
首先,操作员手动操作的不准确性是导致分中问题的主要原因。想象你在黑暗中试图找到一个微小的目标,如果没有合适的工具和技巧,很难做到准确。
其次,模具周边的毛刺也会影响分中精度。这些毛刺就像障碍物,阻碍你找到正确的位置。
再者,分中棒如果有磁性,也会导致分中不准确。磁性分中棒会在金属模具上产生吸引力,从而影响分中的精度。
模具四边不垂直也会导致分中问题。如果模具四边不垂直,那么你在分中时就会遇到困难,因为你的参考点不再准确。
那么,如何改善分中问题呢?其实,解决方法也并不复杂。
首先,操作员在手动操作时要反复进行仔细检查,尽量在同一点同一高度进行分中。这样可以减少人为误差。
其次,模具周边的毛刺需要清理干净。你可以使用油石或锉刀去除毛刺,然后用碎布擦干净,最后用手确认是否平整。
再者,对模具分中前,将分中棒先退磁。可以使用陶瓷分中棒或其他非磁性材料,这样可以避免磁性分中棒带来的影响。
校表检查模具四边是否垂直。如果垂直度误差较大,需要与钳工一起检讨解决方案。
对刀问题:精准测量的挑战
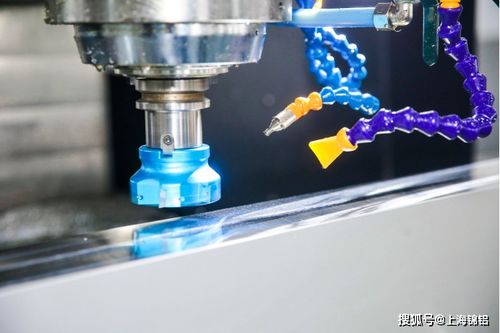
对刀问题是CNC加工中另一个常见的问题,它直接影响加工的精度。那么,对刀问题究竟是如何产生的呢?
首先,操作员手动操作的不准确性是导致对刀问题的主要原因。想象你在黑暗中试图找到一个微小的目标,如果没有合适的工具和技巧,很难做到准确。
其次,刀具装夹有误也会导致对刀问题。如果刀具没有正确地安装在刀柄上,那么在加工过程中就会产生偏差。
再者,飞刀上刀片有误也会影响对刀精度。飞刀本身就有一定的误差,如果刀片选择不当,误差会更大。
R刀与平底刀及飞刀之间有误差也会导致对刀问题。这些刀具之间的误差会导致加工路径偏离预定轨迹。
那么,如何改善对刀问题呢?其实,解决方法也并不复杂。
首先,操作员在手动操作时要反复进行仔细检查,尽量在同一点进行对刀。这样可以减少人为误差。
其次,刀具装夹时要确保刀具